End-of-Line Testing in Automotive Manufacturing
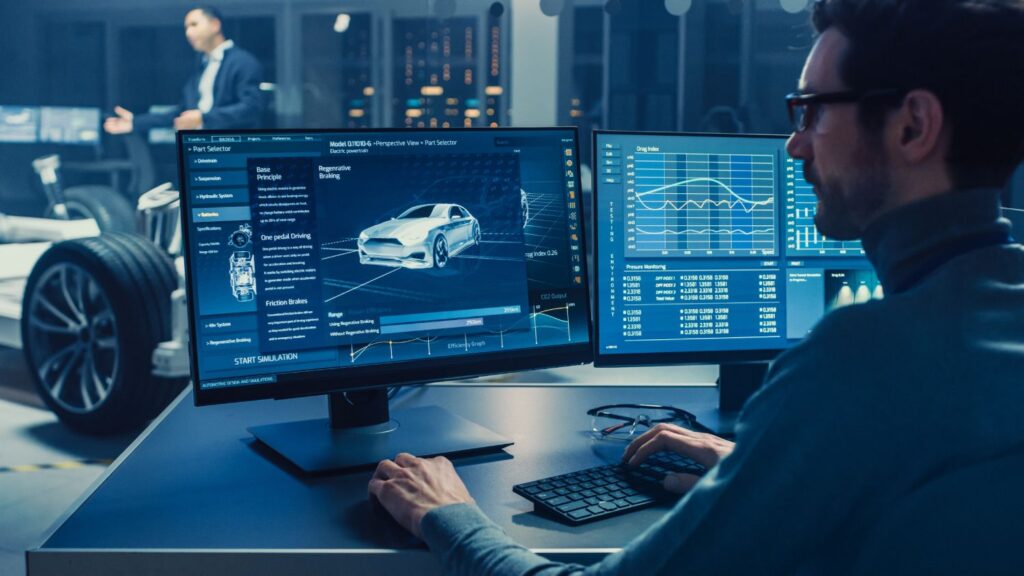
Quality slips resulting in vehicle recalls can devastate automotive OEMs, their contract manufacturers, and their consumers. Drivers depend on their vehicles; even minor manufacturing errors can threaten their livelihoods or place them at risk of injury. When this happens, the OEM’s reputation and bottom line can take a sustainable hit. This has caused many OEMs to implement extensive end-of-line testing for automotive-specific requirements. However, this also places OEMs in a sticky predicament. In order to meet consumer demand for newer, more high-tech features, OEMs must continuously redesign and upgrade their vehicles, potentially rendering their current end-of-line testing obsolete. Most automotive OEMs release new models annually, making reinvestment in new testing systems prohibitively expensive. Test Products Inc. has the solution.
Addressing the Limitations of Automotive End-of-Line Testing
End-of-line testing in automotive applications is an essential part of the quality assurance process; however, it tends to have limitations that can create delays, additional expenses, and product damage. Test Products has spent the better part of four decades working closely with automotive OEMs to develop customized testing solutions that address the following limitations.
Flexibility
The automotive sector is one of the quickest-evolving industries, with an ever-increasing demand for advanced features, such as incorporating the newest technologies that improve safety, reliability, fuel economy, and user experience. Each new feature requires validation to ensure it performs as intended without compromising passenger safety. In some cases, multiple features will require testing throughout the production process. A flexible testing system that allows for easy adjustments and rapid results is key to meeting the fluctuating requirements.
Scalability
The goal for any product, automotive or otherwise, is for demand to increase to the point where manufacturing must scale to meet the new production requirements. When new production lines are added, end-of-line testing can create bottlenecks if it’s not designed to scale in tandem. Ideally, customized testing solutions will include the flexibility to add additional capacity as demand increases. This allows OEMs to increase production much quicker and at reduced costs than if they had to commission additional testing equipment.
Rework Requirements
One of the biggest limitations to end-of-line testing is the inevitable rework requirements when the system catches quality issues. By this time, hundreds, if not thousands, of components and assemblies have already been manufactured. Each unit within that batch must be either scrapped or reworked, both costly and time-consuming processes. Catching quality issues before they reach end-of-line testing with in-process inspection capabilities is critical to preventing this level of complex rework.
Repeatability
This is where The Power of Connection really comes into play. We’re talking about the actual plug-and-socket electrical and network components that connect the product to the testing system. These small and crucial parts are placed under tremendous stress, especially in high-volume settings. Constructed with narrow pins or thin plastic tabs, these connectors require precision for reliability and accuracy. As more units pass through a testing system, these physical connections become damaged or worn, resulting in unreliable accuracy and costly quality slips.
It’s currently standard practice for manufacturers to treat testing connectors as consumable expenses. Over the course of the system’s lifespan, this additional expense can reach dizzying proportions, which can cause less quality-focused manufacturers to postpone replacement until the quality slips become too high to ignore. The key to ensuring consistent repeatability is through durable connectors that anchor securely, provide rapid and accurate results, and then disconnect with minimal effort—all without causing damage to the tester or the product-under-test.
Safety
In automotive end-of-line testing, safety is paramount, not just for testing operators, but also for the end consumer. One of the biggest drawbacks to conventional testing is the risk of damaging the product’s sensitive components during the connecting and disconnecting process. If one pin bends or a single tab snaps off and goes unnoticed, vital safety features cannot be relied on. It’s not unheard of for airbag test equipment to cause unintended airbag deployment due to this damage. In fact, many automotive testing facilities will refuse to test specific systems to avoid the potential liability in the event testing does damage the product. TPI doesn’t shy away from this critical validation, but we embrace our ability to test anything we can connect with.
How Does TPI Overcome These Challenges? With the Power of Connection!
We have leveraged our expertise and experience to develop revolutionary connections that will withstand extensive testing requirements without damaging the product or becoming damaged by high-use applications or careless operators. These custom automotive testing systems rapidly provide reliable validation throughout their extended lifespan. Our tester connections are long-term solutions to improving performance reliability and testing accuracy without continuously investing in replacement components.
To discover the Power of Connection in your automotive end-of-line testing processes, contact the experts at Test Products today!